Impact of Supply Chain Management in Manufacturing
As global supply chains in manufacturing face unprecedented challenges, companies need to adapt and innovate to survive and thrive.
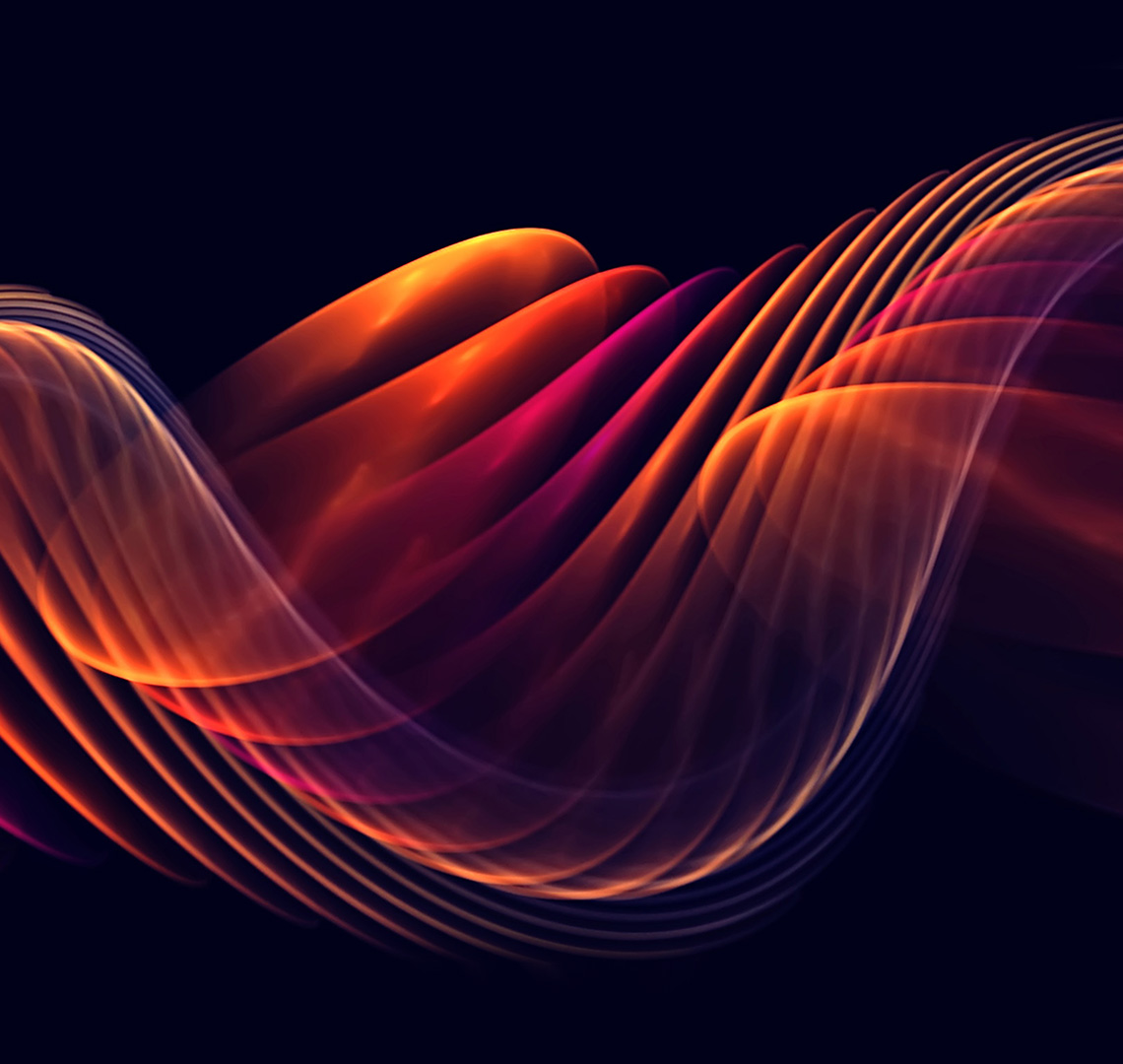
Introduction
The mention of vulnerabilities in global supply chains brings to mind the 2011 earthquake in Japan. Toyota witnessed a staggering 78% production drop due to disrupted supply networks, resulting in massive losses over six months of lost output. This incident prompted the automobile major to restructure its supply chain strategy.
Toyota’s response included sourcing critical components from multiple suppliers, maintaining higher inventories, and strengthening supplier collaboration. These strategic shifts helped the brand ramp up production within two weeks of the April 2016 earthquake.
Today, the challenges manufacturers face have intensified, as geopolitical unrest, climate change, and the complexity of global supply networks have created a volatile and uncertain environment. Companies of all sizes face increased risks, demanding innovative and strategic approaches to manage modern supply chains effectively.
Major Headwinds Facing Today’s Manufacturing Supply Chains
As manufacturing supply chains become more global, disruptions in one part of the world can send ripples across the entire network. Understanding the key obstacles will help manufacturers navigate this climate of persistent unpredictability. Let’s deep dive into some of the supply chain challenges for manufacturers in 2024:
1. Shift from ICE vehicles to EVs
The automotive industry is witnessing a critical transformation led by the shift from well-established internal combustion engines (ICE) to the expanding market of electric vehicles (EVs). However, it is accompanied by its own set of supply chain challenges.
While many ICE components can be reconstructed to support EV production, roughly 25% have to be built from scratch. Certain essential components in ICE vehicles, such as fuel, transmission, exhaust, and cooling systems, are not needed in EVs. That requires suppliers to diversify into EV-related technologies to remain competitive. Sourcing scarce battery minerals, forging new partnerships, and integrating advanced technologies make the EV supply chain a complex and evolving landscape.
2. Semiconductor shortages
The semiconductor shortage has exposed vulnerabilities in the global supply chain, affecting over 100 industries, disrupting production, increasing costs, and pushing companies to reconsider their strategies. The scarcity drove up semiconductor prices, further increasing manufacturing costs and potentially leading to higher consumer prices.
3. Global trade uncertainties
In the past, economic turmoil caused by the pandemic revealed numerous vulnerabilities in global supply chains, highlighting their fragility and the risks associated with reliance on complex, interconnected networks. Rising geopolitical tensions have only exacerbated these concerns, creating uncertainty with unpredictable trade policies and tariffs for supply chain managers. For instance, the ongoing US-China trade war reshaped global supply chains, introducing increased tariffs, delays, and protectionist policies. It tested businesses’ resilience as they had to re-evaluate their supply chain strategies and consider shifting towards diversification.
4. Ocean freight bottlenecks
Ocean freight bottlenecks, stemming from factors like port capacity limitations, pandemic disruptions, and operational inefficiencies, are slowing down global trade. Congestion on ocean highways increases shipping costs and delays the delivery of goods, impacting manufacturing operations and global trade. For example, the repercussions of the six-day Suez Canal blockage in 2021, caused massive traffic, preventing over 60,000 containers of goods from reaching their destinations. This might be a rare event, but experts predict the occurrence of similar incidents, emphasizing the need for resilient supply chain strategies.
5. Rising costs and inflation
Inflation drives up the cost of raw materials and production. Rising labor, energy, and transport costs create a cascading effect throughout the supply chain, posing a significant risk to the existing system. With reduced access to capital due to high interest rates, businesses are exploring various strategies to mitigate the impact. These include prepaying for goods, extending credit lines, negotiating extended delivery windows with suppliers, and downsizing product lines to control expenses.
6. Raw material shortages
The shortage of raw materials due to various economic factors, including geopolitical tensions and a surge in e-commerce demand, has strained global supply networks for manufacturing organizations. The ongoing Ukraine war further escalated this problem by preventing access to potential raw material sources. Moreover, reliance on a limited number of suppliers with few alternatives creates sudden supply chain instability, resulting in production halts and customer dissatisfaction.
7. Climate change and environmental pressures
Climate change poses a longstanding challenge for supply chains, disrupting transportation routes, damaging infrastructure, and halting production, which can lead to delays and increased costs. For example, in 2022, the Yangtze River—accounting for 45% of China's economic output—experienced a severe drought, with water levels falling over 50% below normal. This resulted in shipping closures in several areas.
With consumers' growing environmental consciousness, there is a demand for sustainable products. As a result, sustainability has become a top priority for global supply chains and businesses. This shift presents new challenges for supply chain management, as environmental pressures increase the overall risk and complexity of navigating these intricate networks.
Overcoming Obstacles with Supply Chain Design and Management
A strategic approach to supply chain management is essential for navigating challenges and achieving sustainable growth. Through this approach, businesses can identify risks and address pain points before they escalate into major issues for customers. Let's take a look at these solutions:
1. Cost engineering
Cost engineers bring their in-depth costing knowledge and influence within product teams to enhance the capabilities of manufacturing intelligence software. They assess the costs of supply chain options, allowing organizations to make more cost-effective decisions. However, the supply chain crisis has compelled these engineers to make more immediate estimates to ensure organizations capitalize on scarce opportunities.
2. Strategic sourcing
This approach to supply chain management helps companies secure the best possible value from their purchasing decisions. Through a re-evaluation and improvement process, strategic sourcing empowers organizations to transform their procurement from a transactional function to a strategic business activity. This optimizes supply chains, reduces costs, and enhances quality and efficiency.
3. Supplier risk and quality management
Implementing a supply chain risk management strategy enables companies to build resilience to navigate uncertainty, ensuring business continuity. This approach involves identifying and addressing potential vulnerabilities within a company’s supply chain, minimizing the impact of risks on operations, reputation, and financial performance. As a result, companies can avoid or minimize disruptions, reduce costs, improve quality, and enhance customer satisfaction.
4. Supplier development
With an effective supplier development strategy, companies can establish long-term supplier relationships with transparency to mitigate risk within the supply chain. The approach entails collaborating with strategic suppliers one-on-one to increase capabilities and improve performances in key areas. It benefits the companies and their suppliers, leading to cost reductions, improved product quality, faster delivery times, and the adoption of emerging technologies to build efficiency.
5. Demand planning
Accurate demand planning is a crucial component of the supply chain as it helps companies manage inventory more strategically and maintain profitability. It anticipates demand for a given product and successfully aligns company output through the supply chain without incurring any extra expense. It requires a deep understanding of products and their respective lifecycles, using complex algorithms to analyze historical data, develop supply chain forecasts, and manage trade promotions.
6. Materials management
Materials management is a core function of supply chain management, controlling and managing materials within the company. It involves planning and executing supply chains to meet their material requirements at the right time. It encompasses controlling and regulating material flow while assessing key variables like demand, price, availability, quality, and delivery schedules.
7. Logistics management
Logistics management, another subset of supply chain management, ensures the timely, reliable, and cost-effective movement of goods from the point of origin to that of consumption. The process includes planning, implementing, and controlling the physical movement — including inbound and outbound logistics — of goods and documentation. Key elements include transportation, warehousing, inventory management, and packaging.
Conclusion
To succeed in today’s complex and interconnected manufacturing landscape, companies must reimagine their supply chains. Collaborating with innovation experts who possess the right blend of technology, industry knowledge, and a robust partner ecosystem can streamline this process, enabling businesses to effectively navigate challenges and unlock new opportunities.
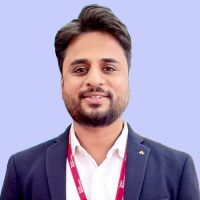
Amit is a Supply Chain professional with over 17+ years of experience optimizing procurement processes, driving cost reductions, and enhancing supplier relationships.
MoreAmit is a Supply Chain professional with over 17+ years of experience optimizing procurement processes, driving cost reductions, and enhancing supplier relationships.
With an MBA and bachelor’s degree in mechanical engineering, Amit has a proven track record of strategic sourcing initiatives that improve operational efficiency and support organizational goals. He is responsible for Strategic Sourcing, Cross-functional Collaboration, Product Development, and Supplier Relationship Management.
Less