Securing the Future of Manufacturing: 12 Golden Rules for Industrial Cybersecurity in the Age of SDM
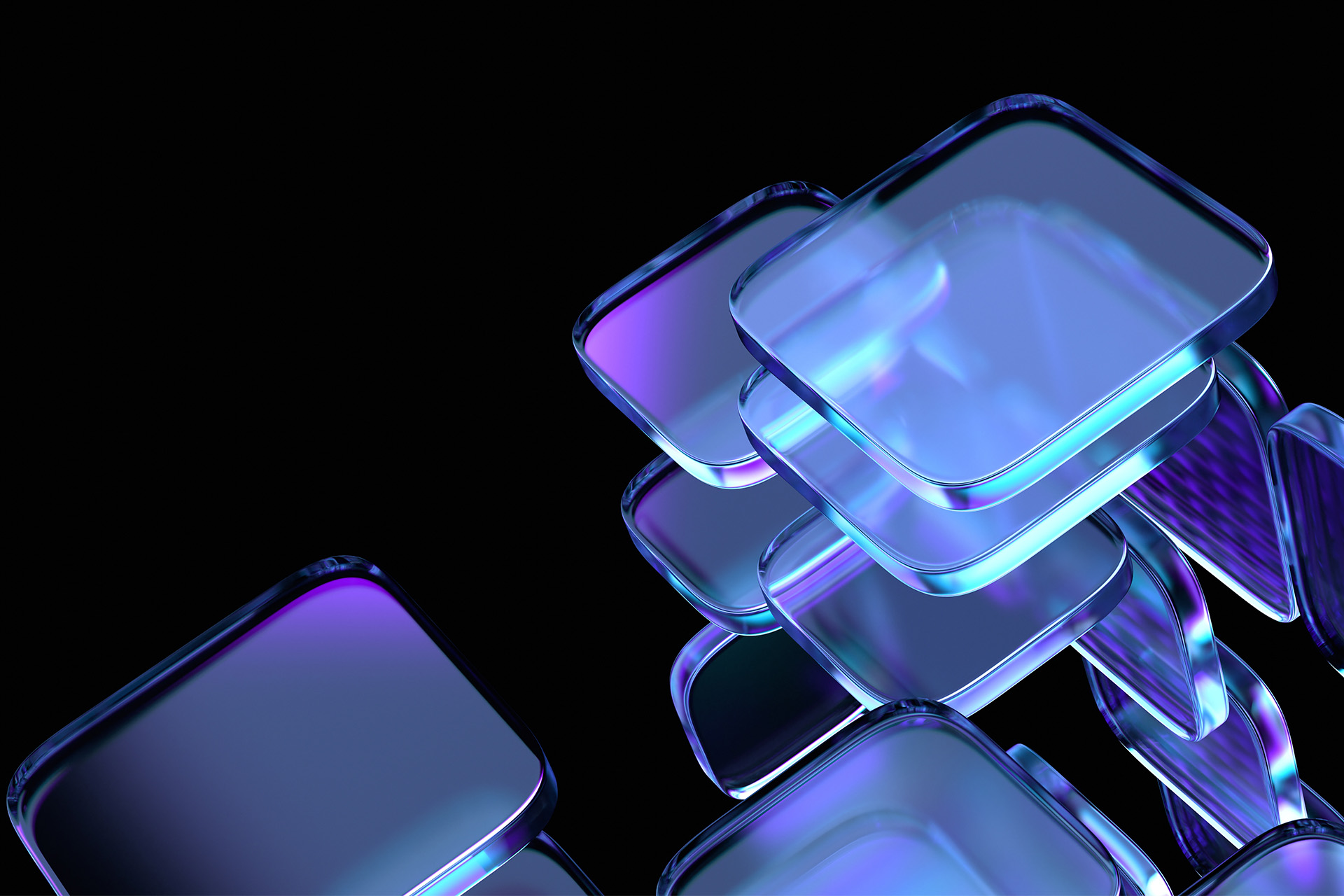
The Dawn of Connected Manufacturing
The manufacturing landscape is transforming rapidly, driven by the rapid adoption of Software-Defined Manufacturing (SDM). This paradigm shift leverages the power of software and data to optimize and control every aspect of the process flow, from planning and design to production and logistics. The result is a more flexible, efficient, and responsive manufacturing environment that can adapt to the ever-changing demands of the global marketplace.
The shift towards Industry 4.0, with its emphasis on interconnectedness and data-driven decision-making, has paved the way for SDM's rise. We're witnessing a convergence of the physical and digital (i.e., phygital) worlds, where machines, sensors, and robots are seamlessly integrated through advanced software systems. This interconnectedness is further enhanced by the Industrial Internet of Things (IIoT), enabling a vast network of smart devices to collect and share real-time data, fueling greater automation and optimization within factories. Future trends like Industry 5.0, where collaborative robots (cobots) and humanoid robots will increasingly support factory operations, will amplify this interconnectedness further, creating even more opportunities for innovation and efficiency.
Cybersecurity Challenges in the Era of SDM
The shift to SDM introduces a new set of cybersecurity challenges for industrial operations. Industrial environments' unique vulnerabilities and increasingly sophisticated cyber threats necessitate a robust and proactive security approach.
Industrial environments often face challenges due to the prevalence of legacy systems that lack built-in security features and are difficult to update. Balancing production demands with security concerns requires a strategic approach, as operational efficiency often precedes security measures.
Furthermore, the complexity of modern industrial environments, with diverse systems and extended supply chains, creates a fragmented security landscape. Integrating various technologies from multiple vendors can hinder the implementation of consistent security practices, and compromised components or software can introduce vulnerabilities.
Meeting evolving regulatory requirements, like NIS2, NERC-CIP, and ISA/IEC 62443, adds another layer of complexity. These standards emphasize the need for robust cybersecurity measures within critical infrastructure and industrial control systems, requiring significant investment in security technologies and expertise.
Addressing these challenges is necessary for the safety, reliability, and productivity of manufacturing operations in the age of SDM. Recognizing the specific vulnerabilities of industrial environments and implementing robust security measures is essential for mitigating risks and building a resilient manufacturing future.
The 12 Golden Rules for Industrial Cybersecurity
To help manufacturers navigate this complex landscape and protect their operations from cyber threats, we've developed 12 Golden Rules for Industrial Cybersecurity. These rules provide a framework for establishing a comprehensive security strategy, enabling manufacturers to embrace the benefits of SDM while mitigating the associated risks.
- Rule 1: Prioritize Cybersecurity from the Start
Embedding security into the development phases of SDM initiatives itself is crucial for long-term success. By incorporating security considerations from the outset, manufacturers can avoid costly retrofits and vulnerabilities that may arise later. A Secure Software Development Lifecycle (S-SDLC) approach, which integrates security into each stage of the software development process, is essential for proactively addressing security risks. - Rule 2: Embrace a Zero-Trust Security Model
In industrial settings, where physical processes are controlled by software and networks, trust should be limited, and verification is paramount. A zero-trust security model assumes no user or device should be trusted implicitly, regardless of location or previous access. This approach necessitates verifying every access request and implementing robust controls to make sure only authorized users can access sensitive systems and data. Multi-factor authentication and least privilege access are crucial elements of this model. - Rule 3: Segment Your Network
Dividing the network into isolated zones or segments for different functionalities (e.g., IT, OT, cloud) is a fundamental security best practice. Network segmentation mitigates the impact of a cyberattack by containing and preventing it from spreading to other critical parts of the system. VPNs, firewalls, and other security tools can limit the potential damage from an attack. - Rule 4: Secure Remote Access and Implement Robust Access Control
Restricting access to data based on roles and permissions is critical for preventing unauthorized access and data breaches. Role-based access control (RBAC) can be implemented to ensure that users only have access to the resources they need to perform their tasks. Strong authentication measures, such as multi-factor authentication, should be employed to verify user identities before granting access. Securing remote access to industrial control systems is crucial, as it can open up significant security risks if not properly managed. VPNs and robust authentication mechanisms should be utilized to protect remote connections. - Rule 5: Regularly Patch and Update Systems
Software vulnerabilities are a significant entry point for cyberattacks. Keeping all systems, including operating systems, applications, and latest security patches is essential for minimizing the risk of exploitation. Implementing a robust patch management program that includes automated patching and regular system updates can significantly reduce the threat surface and enhance the security. - Rule 6: Conduct Continuous Risk Assessment
Continuous risk assessment is paramount for maintaining a robust ICS security posture. This should cover various aspects of the factory environment, including assets, processes, and technologies. A regular risk assessment report should be generated and shared with senior management to ensure appropriate measures are taken to mitigate identified risks. - Rule 7: Implement Intrusion Detection and Prevention Systems
Intrusion Detection and Prevention Systems (IDS/IPS) are crucial in monitoring network traffic for suspicious activity and blocking malicious traffic. These systems can detect and prevent cyberattacks, such as malware infections, denial-of-service attacks, and unauthorized access attempts. Utilizing IDS/IPS can significantly strengthen the security posture of SDM environments and provide an early warning system for potential threats. - Rule 8: Supply Chain Security
Industrial supply chains are critical components of manufacturing operations, and security vulnerabilities in these chains can have significant consequences. Therefore, conducting regular security risk assessments of Original Equipment Manufacturers (OEMs) and suppliers who provide hardware, software, and other components is essential. Additionally, contractual agreements with suppliers should clearly outline cybersecurity requirements to ensure that security best practices are consistently followed throughout the supply chain. - Rule 9: Implement Data Security and Integrity Measures
Protecting sensitive data, such as operational data, intellectual property, and customer information, is paramount for maintaining the integrity and confidentiality of manufacturing operations. Process historians and Manufacturing Execution Systems (MES) within software-defined factories (SDF) often hold this crucial information and require robust protection. Data encryption, secure access, and data loss prevention technologies should be implemented to safeguard sensitive data from unauthorized access, modification, or deletion. - Rule 10: Conduct Regular Cybersecurity Assessments and Audits
Activities such as penetration testing and vulnerability scanning are essential for identifying weaknesses and ensuring effective security controls. Regular audits can help manufacturers identify weaknesses in their security posture and take necessary measures to strengthen their defenses. These assessments help ensure that security controls function as intended and the overall security posture continuously improves. - Rule 11: Develop a Well-Planned Incident Response Plan
A well-defined plan for addressing cyber incidents is necessary to minimize the impact of an attack and ensure a swift recovery. A response plan should outline roles and their respective responsibilities, procedures for incident detection, containment and eradication, and stakeholder communication protocols. A clear plan ensures the organization is prepared to respond effectively to cyber incidents. - Rule 12: Foster a Strong Cybersecurity Culture
Promoting a strong cybersecurity culture within the organization ensures security at all levels. This involves educating and training employees on cybersecurity best practices, promoting a shared responsibility for security, and encouraging employees to report suspicious activity. A robust cybersecurity culture helps create a culture of vigilance and responsibility, minimizing human error and security breaches.
Let’s Welcome the Era of Secured Manufacturing
The future of manufacturing hinges on embracing SDM and effectively managing its cybersecurity risks. Ignoring cybersecurity in this increasingly interconnected and threat-prone environment can have severe consequences, impacting operations, finances, reputation, and even safety. Proactive and comprehensive SDM security is essential for long-term success. Collaboration and information sharing are crucial for enhanced cybersecurity. Manufacturers should leverage the expertise of peers and security professionals to strengthen defenses against evolving threats. Embracing continuous learning will help businesses stay ahead of the threat landscape.
By adhering to these 12 Golden Rules, manufacturers can build robust SDM security, ensuring reliable operations and driving innovation. This safeguards the future of manufacturing, enabling a secure and prosperous industry. The future of manufacturing is connected and intelligent – prioritizing cybersecurity ensures manufacturers navigate this landscape with confidence and build a secure future.
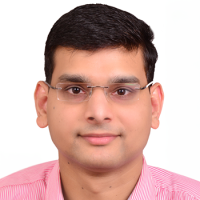
Akhilesh is a cybersecurity architect with 16+ years of diversified experience in the field of cloud security, data security, application security, security operations, identity and access management, OT/IoT security, endpoint security, governance, risk management, and compliance.
MoreAkhilesh is a cybersecurity architect with 16+ years of diversified experience in the field of cloud security, data security, application security, security operations, identity and access management, OT/IoT security, endpoint security, governance, risk management, and compliance.
With a Bachelor's degree in Engineering, Electronics, and Communications, Akhilesh showcases proven experience in leading large, complex cybersecurity projects across multiple streams and geographies, especially around complex phygital products.
Less