The Power of Supply Chain Analytics: Empowering Businesses to Become Resilient, Agile, and Sustainable
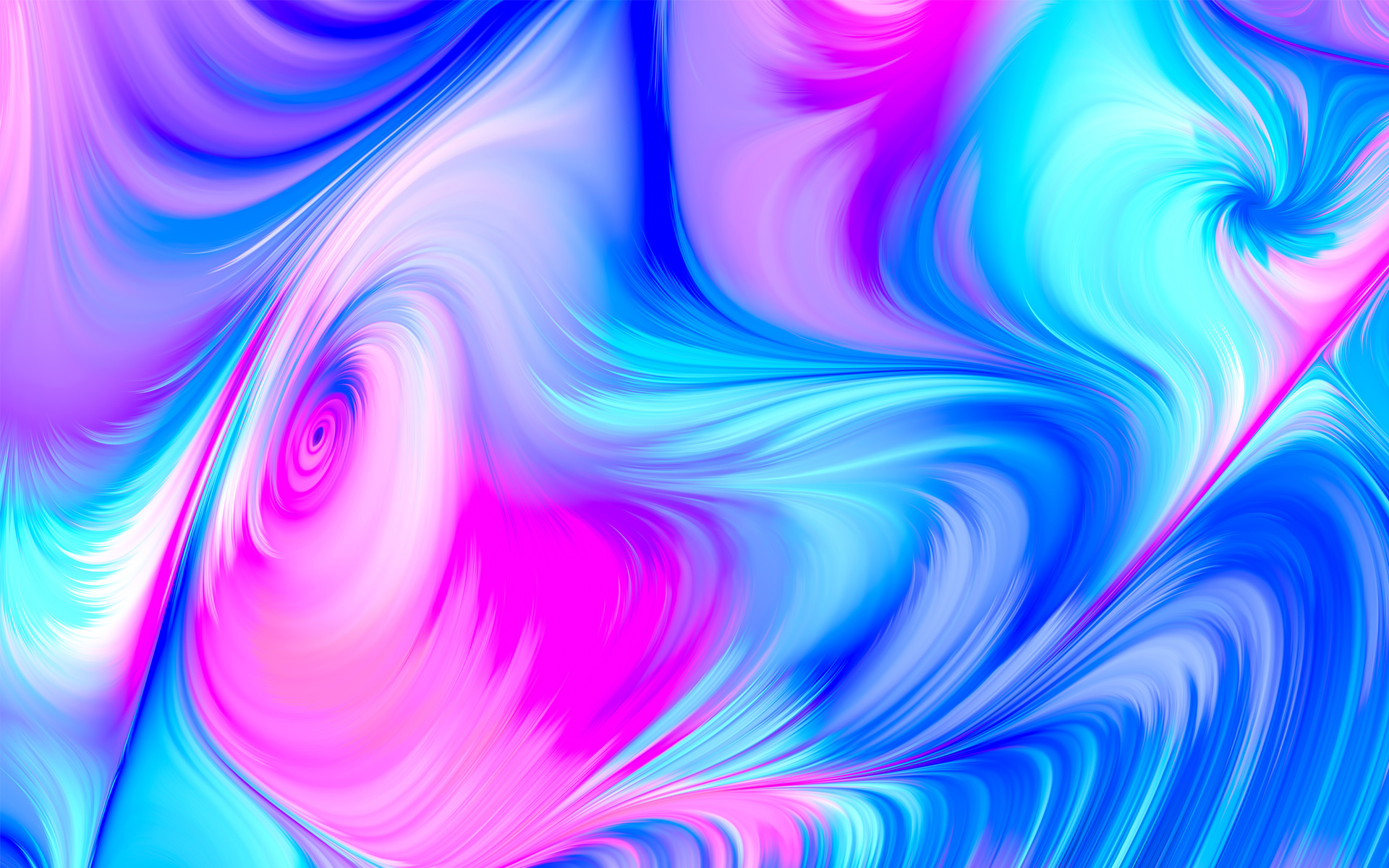
Supply chain disruptions have become the new normal and mitigating risks arising out of these disruptions is key to not just business operations continuity, i.e., protect existing revenue and net profit, but also for future growth opportunities. Improving supply chain directly impacts organizations’ balance sheet, income statement and free cash flows and thus holds a pivotal position in improving the health of every manufacturing company. It is imperative to first understand how existing operations are going on, understand bottlenecks in as-is processes, predict future operations, and take steps to mitigate any challenges for smooth business continuity. It is important for chief supply chain officers and their teams to know what metrics to measure and what are the right tools to capture, predict these metrics, and aid them in quicker and correct decision making.
Introduction to Supply Chain Analytics
Supply chain teams work on all planning and operation activities for the entire movement of material and information right from n tier suppliers to manufacturing to storage in distribution centers, transportation up to final customers, reverse logistics and aftermarket service as well to get the 7 Rs correct – right product, right customer, right location, right price, right time, right quality and right quantity.
Supply chain analytics helps functional users to understand their performance, draw insights and provide tools to run operations more efficiently and effectively. SCM Analytics can be divided into four major analytical buckets – descriptive, diagnostic, predictive, and prescriptive. These types of analytics can be applied in six major areas of supply chain – planning, procurement, production, warehouse, logistics, and aftermarket service.
Descriptive Analytics
Descriptive is the most basic form of analytics which describes functional key performance indicators (KPIs) to show how businesses are performing. KPIs can broadly be classified into safety, cost, service, and quality KPIs. Listed are some of the KPIs in each of the functional areas:
- Planning – Forecast accuracy, bias, fidelity, sales plan vs actual, production plan vs actual, multimodal distribution plan vs actual.
- Procurement Operations – Supplier wise cost, purchase order (PO), cycle time (CT), transport lead time (LT), vendor fill rates, vendor rating on PO and contract adherence, quality rejection.
- Production Operations – Safety total recordable injury rate / lost time incident rate (TRIR/LTIR), throughput, overall equipment efficiency (OEE), inventory holding cost (raw material, work in progress and finished goods), order LT, process CT, scrap.
- Warehouse Operations – Safety, inventory accuracy and turnover, inventory carrying cost, throughput, goods receipt and goods issue cycle time, picking accuracy, dispatch accuracy, excess and dead stock, reject stock.
- Logistics Operations - Transport wise cost, lane wise cost, on time in full (OTIF), capacity utilization, lead time, vehicle quality rejection, and delivery penalty.
- Aftermarket Service Operations – Spare parts spend management, inventory cost, warranty cost, item fill rate and order service levels.
Diagnostic Analytics
It is a way to identify root cause of the problem on why some metrics did not achieve desired results. This is possible by drilldown of descriptive metrics calculation to the lowest possible level and then slice/dice and visualize the data to draw insights. Diagnostic analytics tells business users why it happened. For example – if there is deviation between demand plan vs actual, then diagnostic analytics can tell the user the reason of deviation which could be less accurate forecasting model, inaccurate competition data inputs, sales promotions impact, production failure, transport failure, wrong inventory at wrong place , and so on. Similarly, diagnostic analytics on spend management can help the user understand what is the root cause of deviation which could be few suppliers, transporter performance leading to more expedites, incorrect inventory planning, stockouts, replenishment rate, and lot sizes. For safe operations, any incidents root cause analysis (RCA) helps us take corrective actions and prevent injuries/fatalities in future.
In the same way, diagnostic analytics can be applied to each of the metrics described in descriptive analytics and help the business user unearth the actual root cause of the issue and this helps the decision makers form correct hypothesis and take correct proactive action for future operations in the form of cost reduction strategies, derive automation use cases, correct planning models and parameter settings.
Predictive Analytics
It is form of analytics which uses predictive algorithms to predict business operations. Planning team uses it for demand forecasting and sensing, supplier and transportation risk scores generation, asset preventive maintenance, warranty claim fraud detection and more. Time series algorithms such as regression, Holts Winters; machine learning algorithms such as random forest, support vector machine; and artificial intelligence algorithms such as neural network can be applied to find best fit model for applicable use cases. Image recognition algorithms can be used for material and vehicle quality inspection.
To summarise, predictive analytics use cases are multi fold and it can be used to predict operations metrics and provide a view of projected income statement, balance sheets and cash flows to business owners.
Prescriptive Analytics
These analytics comes after diagnostic analytics and gives actionable recommendations to users’ basis business rules, optimization models, simulations, and metaheuristic models. When scenarios with recommendations are presented to user and decision- making is left to the user, it is called prescriptive analytics. If the decision-making is also done by the system, the supply chains start becoming autonomous. Prescriptive analytics can evaluate multiple what if scenarios and then include recommendations to change material suppliers and transporters, depot inventory rebalance in scenarios of stockout anticipation, production schedule changes per market demand needs, optimize asset parameter settings, safety stock levels settings , and more.
How to Setup Analytical Layers?
Conduct an as-is assessment of current data visibility, people skills levels and tools landscape. Define the data strategy and estimate the technology needed for getting data inputs from multiple planning, transactional and visibility systems for setting up a control tower. Once end to end data is available in data fabric, then first layer is descriptive analytics across all functions of planning, procurement, production, warehouse, logistics and aftermarket service. The second layer will be diagnostic analytics applications. Next will be a predictive layer and on top will be the prescriptive analytics apps. Role- based access can be provided, and persona-based visualizations can be created with drilldown up to lowest level of data for analysis.
Driving Success in Businesses with Analytics
Analytics is an essential layer that sits on top of all data and allows businesses to understand their existing operational performance, identify areas of improvement and take best decisions for the business. Diagnostic, predictive, and prescriptive analytics enable companies to make better data driven decisions and thus their supply chains agile, resilient, and sustainable. By developing use cases across all four layers of analytics, businesses can improve their efficiency, productivity, profitability that, lead to sustainable business growth with better top and bottom lines, healthier balance sheets, and optimum free cash flows.

Biswaranjan has led digital supply chain transformations and brings in rich experience from Tata, Reliance, BASF and Vestas in supply chain planning and operations. He is currently helping manufacturing customers globally in their journey towards supply chain transformation. He holds a degree in Energy (Electrical) Engineering from IIT Kharagpur (2010) and an MBA in Manufacturing and Operations from SPJIMR (2015).