Industry 4.0: How Comparative and Consolidated Insights from Several Factories Enhance KPIs
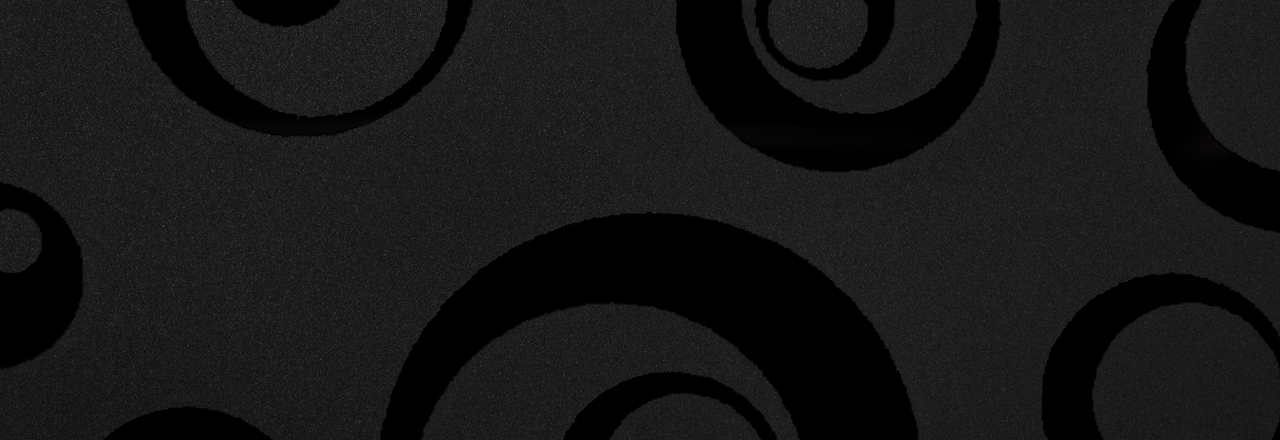
Many industrial companies have already begun their journey towards Industry 4.0 by connecting their machines, obtaining real-time data from them, building dashboards to monitor performance, and utilizing analytics to gain insights.
Even though a specific factory may be able to learn from its own data, it may be missing out on key insights from other factories of a similar nature around the globe. These comparative insights allow us to determine the gap-to-greatness which is the distance between where we are right now and what we want to achieve – greatness by identifying the leading and trailing factories.
They also miss the consolidated insights that enable business leaders to use data to set meaningful goals, rank the best factories and divisions, and reward them. Furthermore, it helps them predict the top and bottom line for the fiscal year.
Understanding Comparative Insights
Comparing KPIs across several dimensions, including locations, factories, manufacturing lines, machines, machine models, products, product variants, and product divisions will provide us with key insights. Comparative insights from several of these dimensions, if not all of them, will offer crucial and useful information that will result in tangible business benefits.
The gap-to-greatness across dimensions provide us with insights about an existing gap as well as the best performance in a related area around the world. The user can delve deep to identify the root cause of the gap and reduce it. This allows for the mutual learning of entities.
Identifying the leading and trailing entities across several dimensions enables us to narrow down the focus area.
Setting Measurable Goals with Consolidated Insights
Consolidated insights can be derived by connecting the factories’ information technology/ operational technology (IT/OT) systems. Business executives can set reasonable goals, evaluate performance, and reward top performers.
It is preferred to establish an enterprise-wide common monitoring mechanism and leverage it to rank and reward the best-performing entities. When evaluating the entities, realistic constraints must be considered, and awards must be given based on actual performance.
By utilizing the data and examining the current constraints, it is preferred to set meaningful targets. It assists in keeping track of the factories' sustainability of operations. It also helps with financial year top and bottom line forecasting.
Boosting KPI’s with Manufacturing Cloud Command Center
Our solution, manufacturing cloud command center, links numerous factories, and business applications like enterprise resources planning (ERP), manufacturing execution system (MES) to provide end-to-end visibility. It leverages a machine learning (ML) powered BI Tool for natural language processing (NLP) based searches, trend identification, anomaly detection, proactive alerting, and self-service visualization that gives users more flexibility.
Business executives will be able to identify KPI measurements that promote efficient operations and those that require improvement. Typically, the solution increases productivity by up to 10%, lowers rework by up to 50%, and reduces breakdown maintenance by up to 20%.
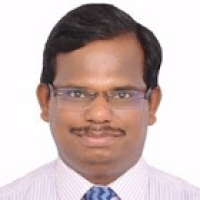
Gurumurugan has over 18 years of experience in the Industry 4.0 areas including digital twin and thread, IIoT, AR/VR, Agile and Lean techniques, digital transformation of manufacturing industry. He has done MBA from IIM Calcutta, and MS from BITS. His experience spans across working in roles such as VP in Connect India, AVP at Traxcn, Infosys, Take Solutions, Tata Motors, and L&T.