Revolutionizing Semiconductor Manufacturing with Digital Twins
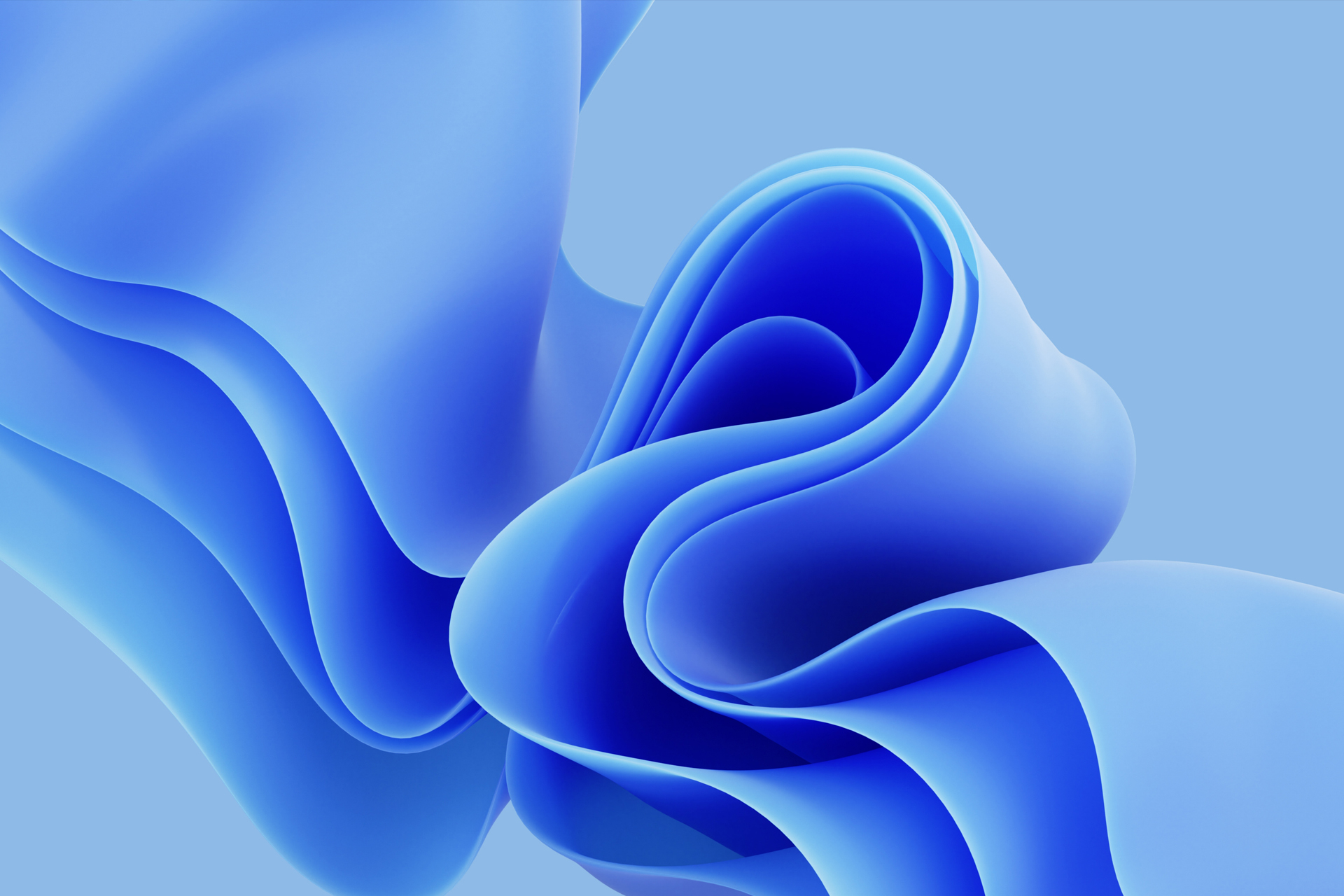
A new era of technological innovation and digitalization is on the horizon for the semiconductor industry. In this fast-evolving environment, digital twins have gained increased traction as a beacon of change. As adoption becomes necessary for companies to remain competitive in semiconductor manufacturing, utilizing digital twins represent both a tactical need and strategic must-have.
Understanding Digital Twins in Semiconductor Manufacturing
A digital twin in semiconductor manufacturing is a holistic virtual model representing the complete flow of production steps, starting from design and simulation to pattern production, fabrication, and testing. This replicates the physical manufacturing environment and allows capturing data in real time from a variety of sources, such as sensors on equipment or supply chain systems.
The three major components of digital twins include a physical object in real space, a simulated object in simulated space, and data and information connecting associations of virtual vs. real objects.
Key Benefits of Digital Twins
One of the key roles of digital twins in manufacturing is offering an end-to-end perspective regarding inefficiencies, bottlenecks, and improvement areas. By identifying opportunities from the complex data obtained from a digital twin, companies can take better action to enhance production processes and decrease downtime, which leads to more cost savings with additional output. Here are some other benefits of digital twins:
Predictive Maintenance
Because semiconductor manufacturing equipment is a high-end sophisticated machine, it’s prone to wear and tear over time. Using predictive analytics and machine learning algorithms, digital twins predict when equipment will fail before any catastrophe happens. This allows companies to preschedule maintenance based on real-time performance data, resulting in lower unplanned downtime and extended longevity of vital assets.
Accelerated Product Development
The semiconductor industry operates on accelerated innovation cycles, requiring rapid product development and time to market. Digital twins facilitate virtual prototyping and simulation, allowing companies to test design iterations and optimize processes in a risk-free environment. By shortening the product development life cycle, companies can bring new semiconductor products to market faster and gain a competitive advantage.
Supply Chain Optimization
Effective supply chain management is critical for semiconductor manufacturers to ensure timely supply of raw materials and components. Digital twins enable real-time supply chain monitoring, potential disruptions identification, and inventory level optimization. By improving supply chain visibility and resilience, companies can mitigate risk and improve responsiveness to market demands.
Applications of Digital Twins in Semiconductor Manufacturing
Digital twins play a key role in optimizing various aspects of semiconductor manufacturing, including manufacturing processes, equipment maintenance, and product design. Their application can be categorized into:
Product Twin: This aspect of digital twins facilitates collaborative and federated design reviews in virtual reality (VR) environments, allowing geographically dispersed teams to collaborate seamlessly. In addition, virtual simulation and verification capabilities allow stakeholders to perform manufacturing, assembly, and service feasibility checks, reducing the need for multiple prototypes and minimizing production times.
Process Twin: The core functions of the process twin are remote monitoring and control of machinery, along with real-time insights into machine health, performance and key performance indicators (KPIs). By leveraging failure prediction and condition-based maintenance (CBM) analysis, semiconductor manufacturers can proactively address issues, minimize downtime, and optimize process efficiency.
Performance Twin: A performance twin closes the loop between new product development/design and parts sourcing, providing invaluable insight into the health and performance of assets and parts. In addition, it offers a deep understanding of customer preferences and needs, allowing companies to tailor their offerings more effectively.
Conclusion
The digital twin technology holds great promise for revolutionizing semiconductor manufacturing. It offers a virtual representation of physical assets, processes, or systems, enabling real-time monitoring, analysis, and optimization. In the semiconductor industry, where the complexity and scale are overwhelming, this technology presents unprecedented opportunities to increase operational excellence and drive innovation across the value chain.
However, successful implementation requires a strategic approach, a robust infrastructure, and a culture of continuous improvement. As the industry continues to evolve, adopting digital twins will be critical to staying ahead in an increasingly competitive environment.
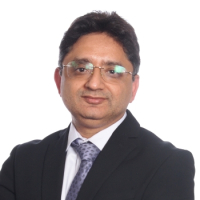
Ateet boasts a rich professional journey spanning over 22 years in the industry, with a robust background in navigating diverse geographies and spearheading strategic initiatives.
MoreAteet boasts a rich professional journey spanning over 22 years in the industry, with a robust background in navigating diverse geographies and spearheading strategic initiatives.
His academic credentials include an MBA from the University of East London and a Business Management Certification from Harvard Business School (HBS). He currently leads growth initiatives for practice build-up for the Semiconductor vertical and Strategic Accounts at Tech Mahindra. Based in the Bay Area, US. He works towards strategically strengthening key partnerships across the value chain of semiconductors, driving innovation and fostering collaboration, along with actively enhancing Tech Mahindra’s association with key industry forums globally.
As a trusted co-pilot to the MD & CEO at Tech Mahindra, Ateet leverages his extensive industry experience to implement transformative strategies, enhancing agility and driving tangible results to the company’s trajectory.
Less