Mill of the Future in CPG industry
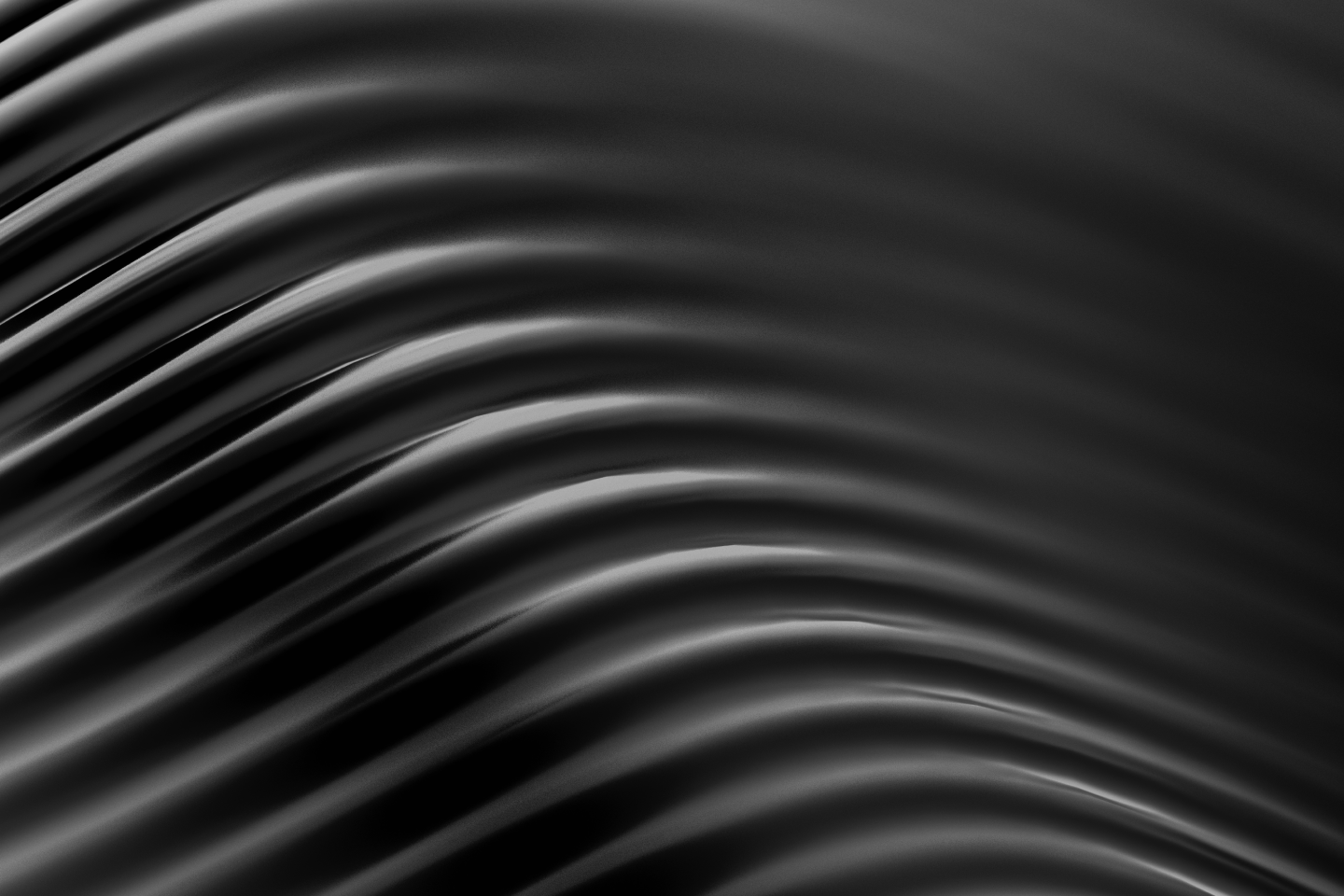
The world of consumer-packaged goods (CPG) industry is currently more volatile than ever. Managing and succeeding in such volatile environment requires efficiency, agility, transparency, and flexibility across all the functions of a company such as procurement, supply-chain, manufacturing, marketing, and sales. Mill of the future aims to drive transformation across the manufacturing plant functions and is driven by harnessing the phygital data deluge, increasing computational power both in cloud and edge and riding on the connectivity accelerator like 5G with guardrails of cybersecurity.
Below are some of the challenges across all dimensions, inflation effecting cost of input, power, wage, and logistics.
- Small or no slab for price hikes due to stiff competition from global and local players.
- Global conflicts and national interests result in trade barriers and supply-chain disruption.
- Increasing demand on sustainability like less plastic, recyclability, carbon footprint, water conservation.
- Need for a transparent supply chain and differentiated products for alternative lifestyles and socially conscious consumers (e.g., organic, vegan, anti-plastic, ethical sourcing)
- Ageing existing skilled and trained work force to be replaced by millennials and Gen Z.
What is Mill of the Future?
Mill of the future leverages technology advancements to infuse a tight collaboration and closed-loop feedback within the factory ecosystem. This ensures timely course corrections, increased efficiencies through dark factories, enhance human-machine interactions, and re-imagined processes among the ecosystem such as suppliers, workforce, and assets.
Mill of the future use-cases leverages one or combination of technologies like industrial IoT, eLTE, 5G, AI/ML, edge, cloud, total security, extended reality, blockchain, and digital twin. While each plant is unique and has its own challenges, following are some of the common high impact mill of the future use-cases.
Mill Twin: Monitor, predict and intervene one or all processes in the plant to prevent quality deviation that leads to high cost of quality. For eg., in paper manufacturing control parameters like line speed, temperature, pH, pressure, moisture, and tension. shall be monitored to avoid web breakage thereby ensuring quality at each stage of the process and minimize overall wastage.
Predictive maintenance: Reactive and periodic planned asset maintenance results in sub-optimal OEE level of the plant or line due to frequent or longer downtime. Predictive maintenance solution prevents unplanned downtime of critical equipment and associated productivity loss. E.g., health parameters like speed, voltage, current, vibration and temperature of the motors in mixing chambers or conveyor systems should be monitored to prevent unplanned motor breakdown.
Smart worker: Empowering stakeholders across the lifecycle of design, manufacturing, logistics with real time insights and data is critical aspects of mill of the future. Some of the use-cases catering to next generation workforce include virtual prototyping, paperless process, immersive virtual training, remote assistance, vision picking and guidance.
ESG through sustainability engineering: Organizations are making pledge towards becoming carbon neutral to carbon negative to water positive. Sustainable technology is a framework of solutions that enable environment, social and governance outcomes. This framework focuses on reducing water and energy consumption across line, product, or plant, optimizing chemical feeds in waste-water treatments, treating greenhouse gas emission, tracking supply-chain carbon trail, enabling circular economy, integrating with carbon offsetting exchange, and enabling dignity to people in the ecosystem.
Road to Success for Adapting Mill of the Future
Every organisation has multiple plants distributed across globe and each plant is unique with respect to the technology landscape, digital maturity, product lines, workforce experience and supplier ecosystem. Successfully adapting the mill of the future across these diverse environments is challenging. Following are few critical aspects to be considered for the success of transformation programs like Mill of the future.
- Common KRA led vision and strategy across organization ensuring continuous investments and collaboration across all functions and regions.
- Dedicated digital program management office with cross functional teams with to-be KPIs (across agility, productivity, cost saving, sustainability, and safety).
- Investing in organizational change management committee to drive training, re-skilling, and process standardization.
- Build Vs. buy decision – identify core and non-core areas to plan own IP or partnership leverage (e.g., paper and pulp companies can consider web breakage prediction model as own IP)
- Converge towards platform approach with modular and reusable templates instead of point products.
- Holistic roadmap and integrated backlogs instead of siloed block with epics covering product design, cognitive experience, plant process, maintenance, warehouse operations, supply-chain, privacy and security, safety, sustainability, and ecosystem collaboration.
- Visualize mill in a box, which is a set of standardized hardware, software, process enabled by canonical data objects, open API’s which can integrate vertically and horizontally.
- Adapt pilot and scale model to ensure maximum impact and value – develop MVP, pilot, validate business benefits, customize, and adapt to other plants.
When it comes to digital initiatives like mill of the future, a holistic approach is critical for the success of manufacturing transformation.
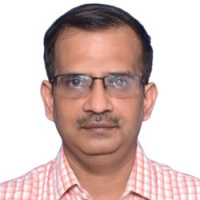
Sanjay is an industry veteran with an experience of 24+ years, leading the design and architecture office of digital product and platform engineering. His breadth of experience covers multiple verticals, manufacturing, logistics, automotive, ISV/IISV, smart cities, retail and CPG.More
Sanjay is an industry veteran with an experience of 24+ years, leading the design and architecture office of digital product and platform engineering. His breadth of experience covers multiple verticals, manufacturing, logistics, automotive, ISV/IISV, smart cities, retail and CPG. Participation in multiple architecture boards reporting to Global CIO’s for multi geo large clients driving organizational technology guideline and blueprinting, cloud strategy, merger and acquisition along with leveraging value stream maps into an enterprise perspective driving continuous strategy, innovation, and sustainability. Sanjay drives executive value stream driven consulting of digital transformation leading towards composable enterprise through digital native assets. He holds master’s degree in Computers from Banaras Hindu University and a bachelor's degree in Statistics from University of Calcutta.
Less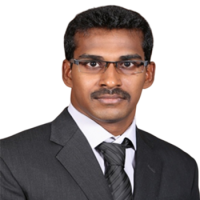
Naveen as a business consultant is responsible for strategizing digital solutions for individual industry verticals. He has 12+ years of experience in digital and embedded technology across various functions pre-sales, alliances, solutioning and consulting. Naveen has done PGDM from the Indian Institute of Management (IIM), Ahmedabad, and holds bachelor’s degree in Electronics and Communication engineering.