Managing Supply Chain Costs Amidst Rising Trade Tariffs: A Consulting Framework
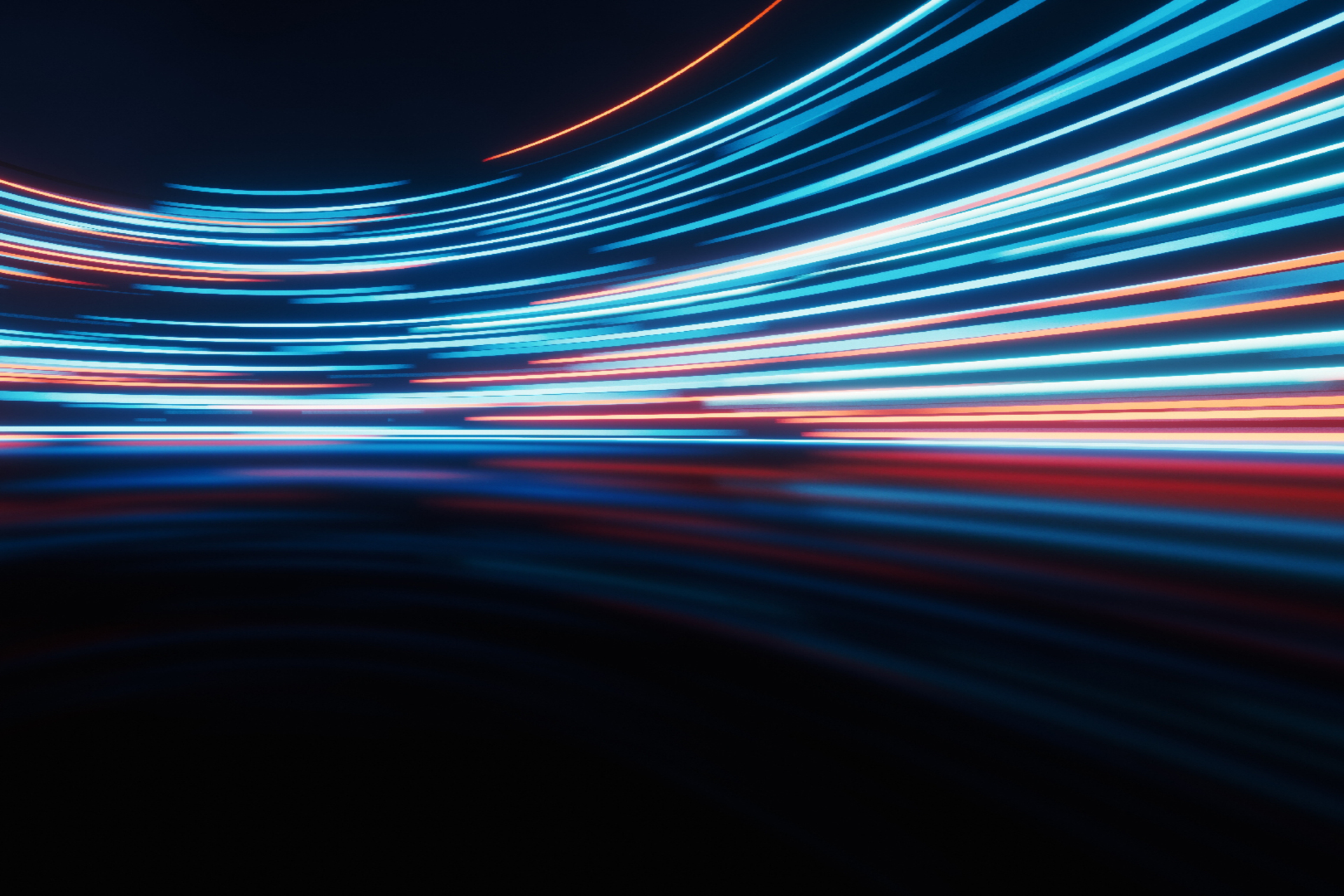
With global trade becoming increasingly unpredictable, rising tariffs strain supply chains. Higher import duties disrupt sourcing strategies, and increased logistics costs force companies to rethink their operations. Without a structured approach to these challenges, they risk losing profitability and competitiveness.
This blog provides a practical framework for companies to assess, mitigate, and optimize supply chain costs in response to rising trade barriers.
Impact of Tariffs on Supply Chains
Before implementing solutions, companies must understand how tariffs affect various aspects of their supply chain:
- Raw Material Sourcing: Higher tariffs increase procurement costs, making raw materials more expensive.
- Manufacturing and Production: Tariffs on imported components raise the overall cost of production.
- Logistics and Distribution: Customs duties, delays, and regulatory hurdles make transportation more costly.
- Pricing and Market Positioning: Companies must decide whether to absorb increased costs or pass them on to consumers.
Measuring the Outcome
The financial consequences of global tariff surges include:
- Landed costs
- Extended lead times due to customs processing
- Reduced profit margins
Analyzing these financial and operational risks is essential to developing an effective cost-management strategy.
Framework for Supply Chain Cost Optimization
The following six-step framework provides a strategic roadmap to optimize supply chain costs:
Step 1: Assessing Tariff Risks and Cost Exposure
- Conduct a thorough cost analysis to pinpoint areas most affected by tariffs
- Map out tariff rates by region and product classification to evaluate cost fluctuations
- Determine total landed cost (TLC), including duties, taxes, and transportation expenses
Deliverable: A tariff exposure report highlighting cost vulnerabilities and financial impact.
Impact: Identify high-risk areas to refine procurement strategies and maximize cost savings.
Step 2: Supplier Diversification and Sourcing Strategy
- Identify alternative suppliers in lower-tariff regions
- Leverage free trade agreements (FTAs) to reduce or eliminate import duties
- Consider nearshoring or reshoring to minimize dependency on suppliers in high-tariff regions
Deliverable: A supplier transition plan outlining cost savings and feasibility for switching suppliers.
Impact: Shifting to suppliers in tariff-friendly areas will maximize cost savings and enhance supply chain resilience by minimizing vendor lock-in.
Step 3: Supply Chain Network Optimization
- Reconfigure manufacturing and distribution hubs to take advantage of duty-free zones
- Implement multi-echelon inventory management to balance costs and stock availability
- Use scenario modeling to simulate tariff fluctuations and evaluate alternative sourcing strategies
Deliverable: A network optimization blueprint with cost-saving projections.
Impact: Minimizes logistics costs by optimizing distribution routes and improving inventory efficiency, reducing storage and carrying expenses
Step 4: Tariff Engineering and Product Classification Optimization
- Reclassify products under lower-duty categories within the Harmonized System (HS)
- Modify materials or components to qualify for more favorable tariff rates
- Use bonded warehouses and Foreign-Trade Zones (FTZs) to defer or minimize duties
Deliverable: A tariff optimization strategy with actionable steps.
Impact: Reduce duties by reclassifying tariffs and adjusting products.
Step 5: Trade Compliance and Regulatory Strategy
- Stay informed about tariff exemptions, duty refunds, and tax incentives
- Automate compliance processes using Trade management software (TMS)
- Strengthen import/export documentation to avoid penalties and shipment delays
Deliverable: A regulatory compliance playbook-specific process improvements
Impact: Reduce customs delays through automation and lower the risk of penalties by avoiding fines per violation.
Step 6: Logistics and Transportation Cost Optimization
- Reroute shipments through low-tariff regions to cut import duties
- Consolidate shipments to minimize customs clearance costs
- Negotiate better rates with logistics providers based on long-term agreements
- Invest in real-time tracking systems to anticipate tariff changes and adapt accordingly
Consulting Deliverable: A freight and logistics cost optimization plan integrated with digital tracking solutions.
Impact: Decreased shipping costs through strategic route planning—improved flexibility to respond to new trade policies.
Leveraging Digital Tools for Cost Efficiency
Technology plays a key role in minimizing the impact of tariffs by improving visibility, efficiency, and automation. As a result, strategic investments in digital solutions give companies a competitive advantage. To capitalize on the benefits, they should consider the following:
- AI and Predictive Analytics: Forecasts alternative sourcing opportunities and tariff risks
- Blockchain and Smart Contracts: Enhances transparency in cross-border transactions
- Cloud-Based Enterprise Resource Planning (ERP) and TMS: Streamline trade compliance and vendor management
- Robotic Process Automation (RPA): Automates customs classification and duty calculations.
Impact: Cut administrative costs through process automation with fewer compliance errors, thereby scaling down the risk of fines and shipment delays.
Future-Proofing Your Supply Chain
Optimizing supply chains can help companies maintain profitability despite shifting global trade patterns. Addressing vulnerabilities, building resilience, and driving efficiency requires a multifaceted approach. Companies turn trade disruptions into strategic opportunities by diversifying suppliers, leveraging trade agreements, optimizing logistics, and harnessing technology.
Is your supply chain affected by rising tariffs? Consult our experts to develop a tailored strategy for a more resilient, cost-efficient supply chain.
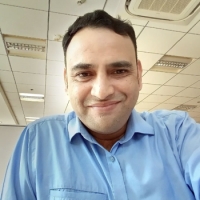
Vishwas is part of Tech Mahindra Consulting and possesses 24 years of professional experience within the Information Technology sector. He holds a Bachelor of Engineering degree and a Master of Business Administration degree from the Indian Institute of Management (IIM), Tiruchirappalli.